-紡績工場見学レポート-
「米ぬか繊維」(綿・レーヨン素材)がどのようにして糸になるのか、その工程を一緒に探っていきましょう。
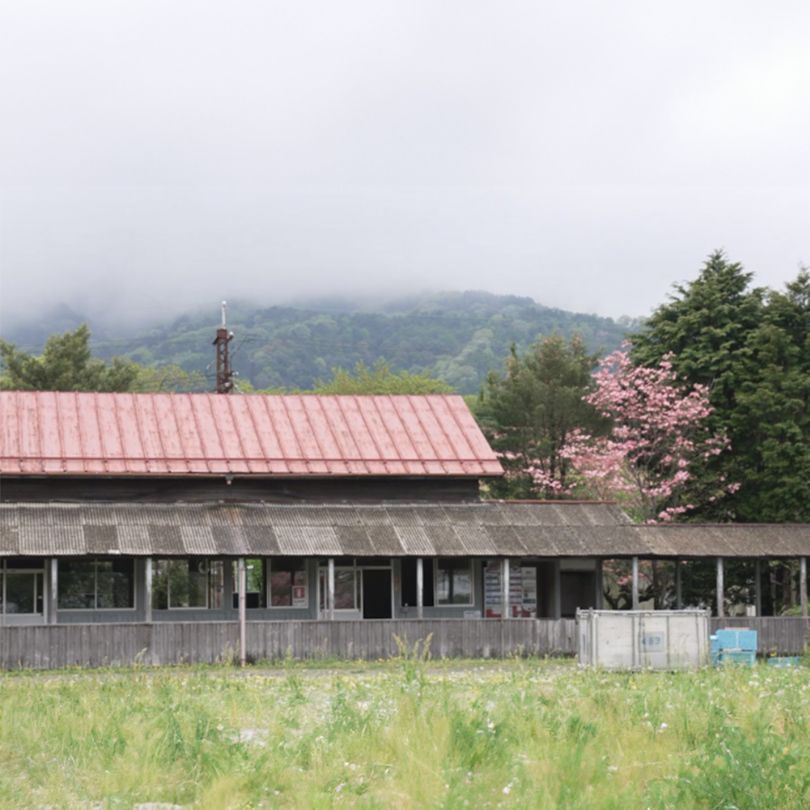
はじめに
先日、株式会社ナイガイテキスタイルさんの紡績工場を見学させていただきました。
工場見学と聞いて少し緊張していましたが、優しいスタッフの皆さんが親切に迎えてくれ、たくさんの質問に丁寧に回答いただきました。
線路沿いに立つこの工場は、昔、汽車で棉(ワタ)を運んでいた名残だそうです。
0. 工場倉庫にて
-運び込まれたレーヨンの棉-
「米ぬか成分が練り込まれたレーヨンの棉」が工場に到着し、糸になるその瞬間を待っています。
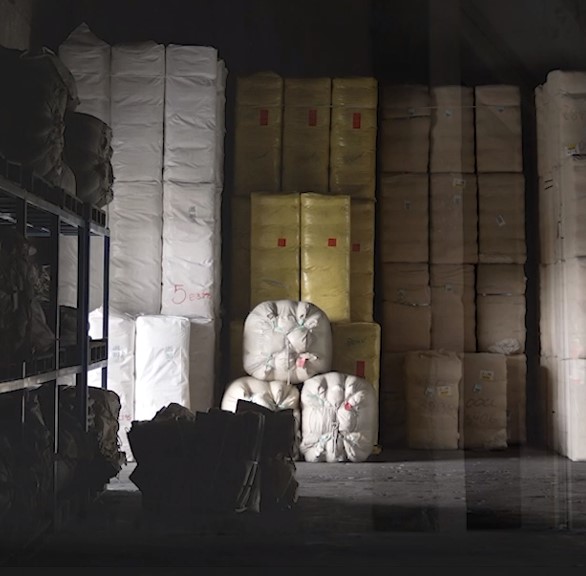
1. 紡績の前準備
-原綿が工場の環境に馴染むまで-
まずは紡績の前に行われる「前準備」です。
工場に届いた綿は圧縮された状態で梱包されていますが、それを開梱し、工場内の温度や湿度に慣らします。この時、綿が膨らんで1.5倍ほどの大きさになります。
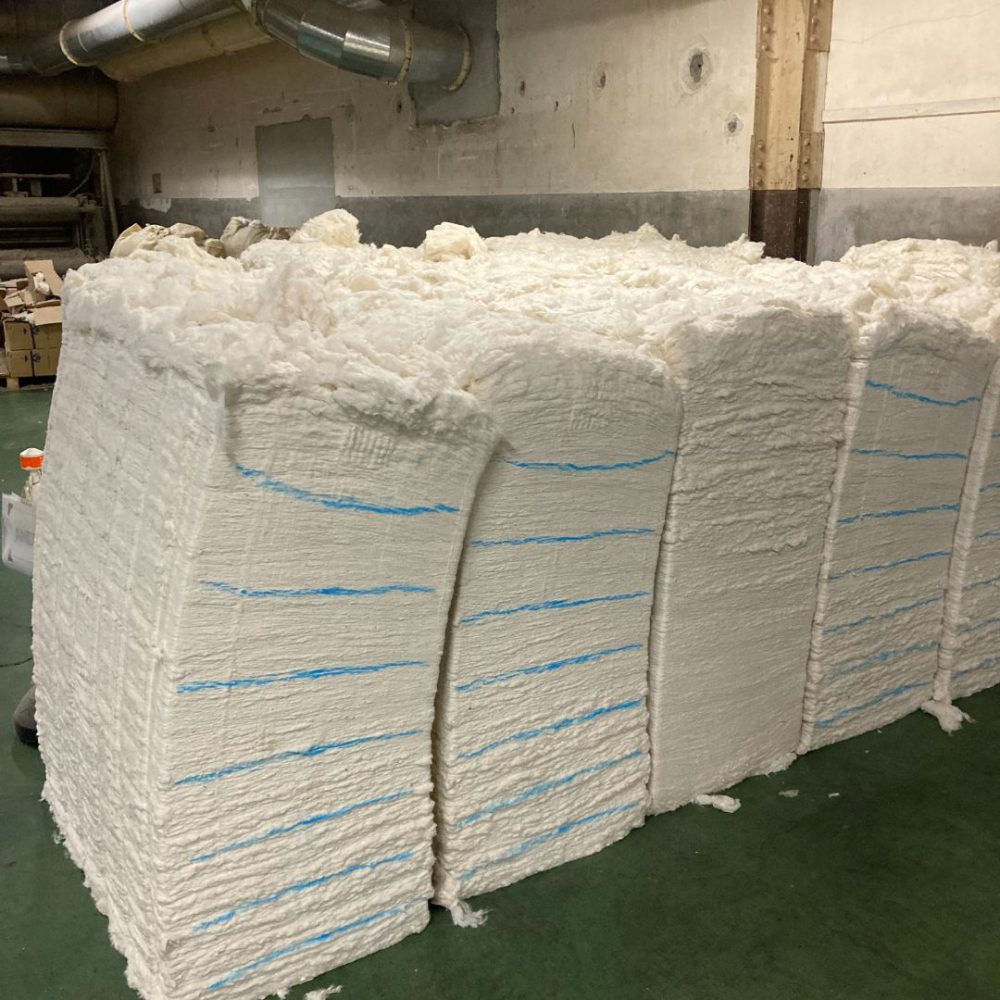
2. 綿をほぐす「混打綿(こんだめん)工程」
次は「混打綿工程」です。
圧縮された綿をほぐし、葉かすや種子片、砂ぼこりなどのゴミを取り除きます。この作業では「混打綿機」という機械が使われます。ここで綿は、まるで魔法のようにふわふわのシート状に変わります。
3. 綿と米ぬかレーヨンの「調合(ちょうごう)工程」
この工程では、「綿」と「米ぬかが練り込まれたレーヨンの棉」を混ぜ合わせます。
まずは計量器付きコンベアを使って正確な量を計り混ぜ合わせます。その後、「ストックビン」という特別な部屋に移され、空気中で舞い上がりながら混ざり合います。
この精密な調合と何度も混ぜ合わせる工程こそが、品質を保つ秘訣です。
※混ざり具合が分かるように、黒に染めた綿を使用しています。
(米ぬか繊維ではありません。)
4. 糸の品質を決める「カーディング工程」
ここで糸の品質が決まる!と言われる重要なステップです。
繊維の長さがバラバラだと糸をつくりづらい為、カード機(梳綿機)と呼ばれる機械を使い、櫛(くし)のようなものでとかすことで短い繊維や小さなゴミを取り除きます。
残った長い繊維をガーゼのように引き伸ばし、「カード・スライバー」と呼ばれる一本の太いひも状に形成します。
5. 高級な仕上がりを生む「コーミング工程」
高級糸を製造する場合に必要となる工程、「コーミング工程」では、さらに短い繊維やゴミを徹底的に除去し、繊維を揃え、再度スライバーに形成します。この工程が加わることで、繊維が均一になり、より滑らかで高品質な糸が作られます。
6. 8本のスライバーを1本にする「練条(れんじょう)工程」
次に行われるのは「練条工程」。
ここでは、出来上がったスライバー(引き延ばした繊維)を8本束ねてさらに引き延ばし、太さのムラをなくします。
7. 糸に撚り(より)をかけながら引き延ばす「粗紡(そぼう)工程」
練条スライバーは、直接糸をつくるには太すぎます。
そこで、更に引き伸ばして細くします。
しかし、ひっぱると簡単に抜けてしまう為、糸の中の1本1本の繊維が絡み合うように、ここで初めて撚りとよばれるねじりをかけています。
8. 完成間近!糸の太さが決まる「精紡(せいぼう)工程」
「精紡工程」では、それをさらに引き伸ばし、所定の太さに細くし、撚りをかけます。
9. 最終仕上げ「巻糸(まきいと)工程」
最後の「巻糸工程」では、最後の「巻糸工程」では、精紡された糸のムラやゴミを除去しながら巻き直します。
この後、ブラックライトを当て検品をし、最終的な形態に仕上げます。この完璧な仕上がりを目指す姿勢が、ナイガイテキスタイルさんのこだわりです。
まとめ
-米ぬか繊維が糸になる感動の瞬間-
見学を通じて、米ぬか繊維が「糸」になるまでの工程には、多くの工夫と技術が詰まっていることを知り、夢中になってしまいました。そして、この一連の工程を経て、棉(ワタ)から美しい糸へと変わっていく様子には感動を覚えました。
次に、この糸は染色や撚糸の工場へと運ばれ、本社工場での編立へと繋がっていきます。
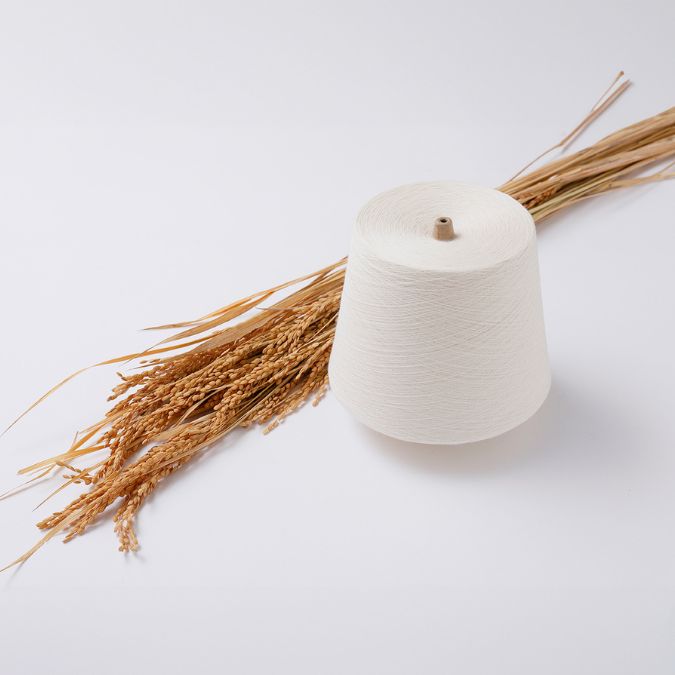
〈鈴木靴下の最新情報はこちら〉
🌾店舗情報はこちら
💭LINEお友達登録はこちら
🧦オンラインショップはこちら